Safety Matches
Safety Matches

A match is a tool for starting a fire. Typically, matches are made of small wooden sticks or stiff paper. One end is coated with a material that can be ignited by frictional heat generated by striking the match against a suitable surface. Wooden matches are packaged in matchboxes, and paper matches are partially cut into rows and stapled into matchbooks. The coated end of a match, known as the match “head”, consists of a bead of active ingredients and binder; often colored for easier inspection. There are two main types of matches: safety matches, which can be struck only against a specially prepared surface, and strike-anywhere matches, for which any suitably frictional surface can be used.Quality Control: The chemicals for each portion of the match head are weighed and measured exactly to avoid any variation in the match composition that might affect performance. Operators constantly monitor the operation and visually inspect the product at all stages of manufacture. In addition to visual inspection and other normal quality control procedures, match production requires strict attention to safety. Considering that there may be more than one million matches attached to the perforated belt at any time means that the working environment must be kept free of all sources of accidental ignition.
Cutting the Matchsticks
- Logs of white pine or aspen are clamped in a debarking machine and slowly rotated while spinning blades cut away the outer bark of the tree.
- The stripped logs are then cut into short lengths about 1.6 ft (0.5 m) long. Each length is placed in a peeler and rotated while a sharp, flat blade peels a long, thin sheet of wood from the outer surface of the log. This sheet is about 0.1 in (2.5 mm) thick and is called a veneer. The peeling blade moves inward toward the core of the rotating log until only a small, round post is left. This post is discarded and may be used for fuel or reduced to wood chips for use in making paper or chipboard.
- The sheets of veneer are stacked and fed into a chopper. The chopper has many sharp blades that cut down through the stack to produce as many as 1,000 matchsticks in a single stroke.
Treating the Matchsticks
- The cut matchsticks are dumped into a large vat filled with a dilute solution of ammonium phosphate.
- After they have soaked for several minutes, the matchsticks are removed from the vat and placed in a large, rotating drum, like a clothes dryer. The tumbling action inside the drum dries the sticks and acts to polish and clean them of any splinters or crystallized chemicals.
- The dried sticks are then dumped into a hopper and blown through a metal duct to the storage area. In some operations, the sticks are blown directly into the matchmaking facility rather than going to storage.
Forming the Match Heads
- The sticks are blown from the storage area to a conveyor belt that transfers them to be inserted into holes on a long, continuous, perforated steel belt. The sticks are dumped into several v-shaped feed hoppers that line them up with the holes in the perforated belt. Plungers push the matchsticks into the holes across the width of the slowly moving belt. A typical belt may have 50-100 holes spaced across its width. Any sticks that do not seat firmly into the holes fall to a catch area beneath the belt and are transferred back to the feed hoppers.
- The perforated belt holds the matchsticks upside down and immerses the lower portion of the sticks in a bath of hot paraffin wax. After they emerge from the wax, the sticks are allowed to dry.
- Further down the line, the matchsticks are positioned over a tray filled with a liquid solution of the match head chemicals. The tray is then momentarily raised to immerse the ends of the sticks in the solution. Several thousand sticks are coated at the same time. This cycle repeats itself when the next batch of sticks is in position. If the matches are the strike-anywhere kind, the sticks move on to another tray filled with a solution of the tip chemicals, and the match ends are immersed in that tray, only this time not quite as deeply. This gives strike-anywhere matches their characteristic two-toned appearance.
• After the match heads are coated, the matches must be dried very slowly or they will not light properly. The belt loops up and down several times as the matches dry for 50-60 minutes.
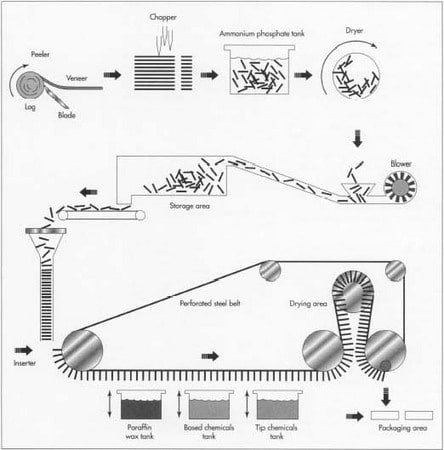
SPECIFICATION OF SAFETY MATCHES | |
---|---|
Standards | EN 1783:1997 Standards or BIS or any other Standards |
Size | 51x35x14 mm, 52x35x14, 53x35x12 mm |
GSM of Outer Box | 280 GSM, 290 GSM, 300 GSM, 320 GSM |
GSM of Inner Box | 270 GSM |
Splints | Russian Splints, Popular Splints or Indian Matti Splints |
Splints Dimension | 42x2x2 mm |
No of Match Sticks in each box | 40 or 45 |
Match Head Colour | Brown or Green or Red or Blue |
10â Packing | Printed Paper or BOPP Film or Cellophane Paper |
100â Packing | Shrink Packing or Polybag |
1000â Packing | Corrugated Fibre Containers in 3 Ply or 5 Ply |
Bar Code Label | 10”s Packing or 100”s Packing as intended by buyers |
Filling of Sticks | Online Machines |
Direction of Match Heads | All appear in one direction |
Raw Materials
Straight grained wood, usually white pine or aspen.
Ammonium phosphate and Paraffin wax for the treatment of wood.
Antimony trisulfide and potassium chlorate for the match head.
Powdered glass and other inert materials for better friction and burning rate.
Animal glue for binding ingredients.
Zinc oxide for coloring of the match head.
Sulfur, rosin, small amount of paraffin wax and phosphorus sesquisulfide for the base of the match.
Water-soluble dye for coloring of the base.
Striking surface contains red phosphorus, powdered glass, and an adhesives (gum arabic or urea formaldehyde)
Cardboard for match boxes and match books.
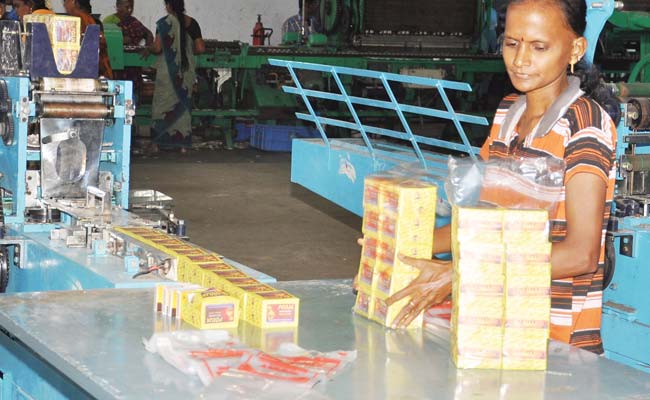
Packaging the matches

- The cardboard inner and outer portions of the matchboxes are cut, printed, folded, and glued together in a separate area. If the box is to contain safety matches, the chemicals for the striking strip are mixed with an adhesive and are automatically applied to the outer portion of the box.
- When the matches are dry, the belt moves them to the packaging area, where a multi-toothed wheel pushes the finished matches out of the holes in the belt. The matches fall into hoppers, which measure the proper amount of matches for each box. The matches are dumped from the hoppers into the inner portions of the cardboard match boxes, which are moving along a conveyor belt located below the hoppers. Ten or more boxes may be filled at the same time.
- The outer portions of the matchboxes move along another conveyor belt running parallel to the first belt. Both conveyors stop momentarily, and the filled inner portions are pushed into the outer portions. This cycle of filling the inner portions and pushing them into the outer portions is repeated at a rate of about once per second.
- The filled match boxes are moved by conveyor belt to a machine, which groups them and places them in a corrugated cardboard box for shipping.